THESYS
Advanced thermal management system
Project description
Airbus is focused on enhancing its technological capabilities to develop a more sustainable and efficient aircraft, featuring advanced capabilities, higher manufacturing cadence, and reduced recurring costs. This will increase customer value while reducing fuel consumption, CO₂ emissions, and airline operating costs. The THESYS project paves the way toward achieving significant emission reductions in Airbus aircraft in the near future.
Specifically, the project concentrates on the maturation of low-emission propulsion technologies, along with the systems and components required to validate their reliability within the aeronautical domain.
Funding bodies
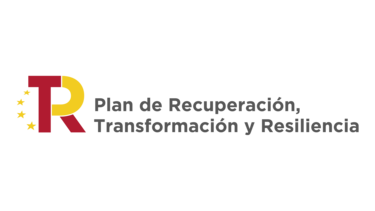
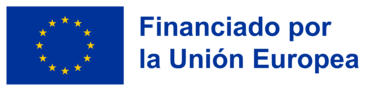
The thermal management challenge for low-emission propulsion
Challenge
One of the major technical challenges of fuel cell systems is the significant amount of heat they generate, which must be managed effectively. Therefore, THESYS aims to design an advanced thermal management system capable of extracting substantial amounts of heat to maintain the fuel cell within optimal operating temperature conditions.
To achieve this, innovative thermal management technologies will be researched to surpass the current state of the art. These technologies will be implemented within a complete electric propulsion system, addressing integration and flight challenges.
As a result, a safe thermal management system will be tested to support the fuel cell, integrating it into a full propulsion system, a first for Spain. Additionally, advanced simulation tools, validation methodologies, and control approaches will be provided. Finally, the operational and maintenance principles of the thermal management system will be demonstrated in practice.
Innovative thermal management for hydrogen-powered aircraft
Solution
The solution involves integrating a thermal management system into hydrogen-powered aircraft. This system includes a primary channel and two secondary channels for heat dissipation, along with additional heat exchangers for power electronics. Atmospheric air is used to cool the hydrogen fuel cell coolant, and air flow is regulated through movable surfaces. Additionally, a secondary cooling loop is required for the electronics and other components. Additive Manufacturing (AM) technology will be utilized to create compact and efficient heat exchangers.
These innovations aim to reduce the weight and maintenance of the system, while improving efficiency and reliability, ultimately contributing to the reduction of emissions in aviation.
Benefits
- AOSL aims to become the leading driver of the hydrogen-based commercial aircraft industry, fostering the creation of high-value-added jobs within the company and its suppliers.
- Key capabilities will be developed to maintain technological sovereignty in Europe, ensuring continued global competitiveness.
- The simplification of the cooling system and the use of appropriate materials reduce maintenance requirements.
- The integration of real-time control systems enhances the efficiency and adaptability of the cooling system based on flight needs.
- The use of Additive Manufacturing (AM) technology to create components with complex and compact geometries reduces time, costs, and material waste.
- By allowing air and liquid collectors to be integrated into a single piece, the efficiency and integration of the cooling system are improved.
- Designing components that fit perfectly within the available space on the aircraft reduces air resistance and fuel consumption.
- Design flexibility also facilitates the creation of anchors and structural joints, allowing for the manufacturing of components in a single piece.
- AM technology enables the incorporation of elements to reduce noise, enhancing comfort both inside the aircraft and at airports.