HERWINGT
Hybrid Electric Regional Wing Integration Novel Green Technologies
Project description
HERWINGT aims to design a novel wing, ideal for the future hybrid-electric aircraft of the Regional segment, and to develop architectures, structures, and technologies allowing higher integration of electric systems.
Target is a 50% fuel burn reduction, at the aircraft level, in three different ways:
- Developing state of the art wing configurations and improved aerodynamics leading to drag reduction and enabling a fuel burn reduction of 15% at the wing component level.
- Wing structures, more integrated systems, and new material technologies resulting in a weight reduction of 20% at the component level.
- The development of technologies equipping the wing with fuel systems that are compatible with Sustainable Aviation Fuels (SAF).
By 2025, HERWINGT also commits to delivering:
- Digital twins and a life cycle assessment (LCA) of the components, subsystems, and full wing systems compatible with the reference aircraft digital framework and requirements.
- Α roadmap toward the wing full-scale demonstration at aircraft level with a first flight.
Follow our project news on our LinkedIn page
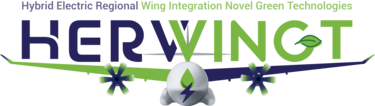
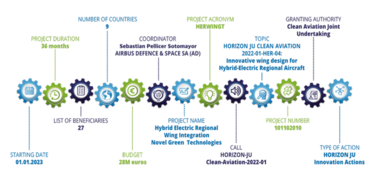
Key enabling technologies of HERWINGT
Challenge
In order to deliver an innovative wing concept towards a significant fuel burn and mass reduction targets, the following key enabling technologies will be addressed in the project:
- Multifunctional and new materials selection for aeronautical use, that can allow us to reduce weight and address highly integrated structures, such as liquid resin infusion, thermoset and thermoplastic, enabling out of autoclave manufacturing processes.
- Development of new structural concepts and architectures with high integration of different elements of the structure in order to minimize, even eliminate, the need of joints and bondings.
- Structure health monitoring systems development for structural integrity prevention and damage anticipation that can allow us to design with less thickness and then less mass
- More electric systems integration, such as an ice protection system based on induction technologies to enable the possibility to integrate this system into the structure minimizing the weight and drag penalties
- New sensors, sealants and materials technologies for Sustainable Aviation Fuels (SAF) in order to prepare the future fuel systems compatible for a broad SAF specification.
- Aerodynamic drag reduction due to high aspect ratio, morphing control surfaces with optimized flight control laws, and improved laminarity of the wing component.
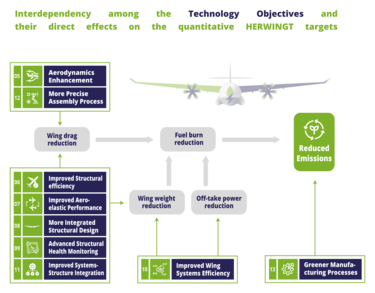
Technology Demonstrators
Solution
The technologies to be developed are planned to be matured until TRL5 by the end of 2025 by means of demonstrators. Then, a complete set of physical and virtual demonstrators is defined to determine which technologies are expected to be matured at each demonstrator.
Fuel burn reduction by means of wing performance
Benefits
The benefits of developing these technologies by means of demonstrators is the maturation up to TRL5 of those technologies elected to be feasible to be applied onto a real wing with good forecasts of certification, and that can deeply impact in terms of wing weight reduction and aerodynamic efficiency improvement in order to reduce the fuel consumption.